Vous connaissez bien le monde de la blanchisserie hospitalière, où vous opérez depuis bientôt 30 ans. Pourriez-vous nous en parler ?
José Machado : Ma première incursion dans ce secteur date en effet de 1987, pour ensuite se poursuivre sur la gestion d’un petit ESAT de 250 kg/jour, structure que j’ai fait évoluer à 750 kg/jour, jusqu’à me retrouver, en 2011, coresponsable d’une unité de 16 tonnes/jours pour le CHU de Toulouse sous le statut d’ingénieur en chef. Je suis toutefois, à la base, titulaire d’un CAP de mécanicien pour machines textiles et d’employé de laboratoire de recherche textile. Pour légitimer mon positionnement sur des postes d’ingénieurs, j’ai donc obtenu il y a quelques années un Master 2 en gestion des établissements sociaux et médico-sociaux. Ce grand écart a été possible grâce à une validation partielle du diplôme CAFDES à travers une validation des acquis de l’expérience et, en mai 2023, j’ai pris le poste d’ingénieur responsable de la production pour le GCS Blanchisserie du Grand Clermont. Je me suis, en parallèle, investi auprès du comité URBH Auvergne, et ai d’ailleurs posé ma candidature pour rejoindre le conseil d’administration de l’association URBH nationale.
Pourriez-vous nous présenter le GCS Blanchisserie du Grand Clermont ?
Dans sa version actuelle, la blanchisserie a été créée en 2008 pour, à l’origine, desservir uniquement les trois établissements du CHU de Clermont-Ferrand. En 2010, elle s’est transformée en GCS et traite désormais aussi le linge des CH Guy Thomas à Riom, Eugène Clémentel à Enval, et Sainte-Marie à Clermont-Ferrand, ainsi que celui des 8 EHPAD du CCAS de Clermont-Ferrand – soit entre 15 et 16 tonnes/jour, toutes typologies de linge confondues. Opérée par 63 agents, elle dispose d’outils de production entièrement automatisés, disposant par exemple – et c’est là une particularité notable – d’un stockeur dynamique alimenté par robot. Autre spécificité, il s’agit de l’une des dernières blanchisseries hospitalières de France faisant l’objet d’un bail emphytéotique, avec un partenaire chargé de la maintenance de ses équipements et de la gestion de son parc immobilier.
Quels projets avez-vous portés depuis votre arrivée ?
J’évoquerais en premier lieu tout ce qui a trait à la responsabilité sociale et environnementale (RSE), qui représente une tendance de fond dans le monde de la santé. J’ai ainsi mené plusieurs actions dès mon arrivée pour réduire notre empreinte environnementale, avec déjà des résultats tangibles. Par exemple, en revoyant le réglage des brûleurs et en limitant le chauffage lors des périodes d’absence des équipes, nous avons pu réduire nos consommations énergétiques de 17 % en un an seulement. Les consommations d’eau en usine globale sont pour leur part passées de 5,7 litres à 4,6 litres, grâce à l’abandon de la lessive en poudre au profit de la lessive liquide, et surtout à la rationalisation du taux de chargement des alvéoles lors du tri du linge. En matière de réduction des déchets, nous avons confié à une structure de réinsertion, la transformation des draps réformés en taies d’oreillers, avec déjà la production d’un premier lot de 5 000 unités. Il nous a en effet semblé dommage de jeter des textiles qui ont conservé la majorité de leurs caractéristiques de tenue, alors qu’ils pourraient servir d’autres usages.
Auriez-vous d’autres pistes sur cette question spécifique des déchets ?
Toutes les blanchisseries industrielles sont forcées d’y réfléchir : bien que nous ne soyons pas encore directement taxés sur les volumes de déchets produits, les coûts d’évacuation ont explosé et nous imposent de chercher des alternatives. Plusieurs options existent aujourd’hui pour la valorisation des textiles réformés, y compris en décomposant les fibres par cardage afin de récupérer la matière première. Mais les coûts de récupération et de transformation sont actuellement refacturés aux blanchisseries, qui ne bénéficient ici d’aucune aide financière. Valoriser nos déchets textiles augmente, in fine, nos coûts de production, ce qui n’est clairement pas incitatif. Et ce sont loin d’être les seuls déchets produits par nos activités ! Ainsi, en 2025, nous essayerons de supprimer les emballages plastiques dans lesquels nous sont aujourd’hui retournés les bandeaux de nettoyage des sols, gorgés d’eau. En remplaçant les modèles existants par des bandeaux ultra-fins, dont les capacités de rétention de l’eau sont donc sensiblement moindres, nous pourrions envisager de nous passer de ces sacs, qui représentent 8 tonnes de déchets par an.
José Machado : Ma première incursion dans ce secteur date en effet de 1987, pour ensuite se poursuivre sur la gestion d’un petit ESAT de 250 kg/jour, structure que j’ai fait évoluer à 750 kg/jour, jusqu’à me retrouver, en 2011, coresponsable d’une unité de 16 tonnes/jours pour le CHU de Toulouse sous le statut d’ingénieur en chef. Je suis toutefois, à la base, titulaire d’un CAP de mécanicien pour machines textiles et d’employé de laboratoire de recherche textile. Pour légitimer mon positionnement sur des postes d’ingénieurs, j’ai donc obtenu il y a quelques années un Master 2 en gestion des établissements sociaux et médico-sociaux. Ce grand écart a été possible grâce à une validation partielle du diplôme CAFDES à travers une validation des acquis de l’expérience et, en mai 2023, j’ai pris le poste d’ingénieur responsable de la production pour le GCS Blanchisserie du Grand Clermont. Je me suis, en parallèle, investi auprès du comité URBH Auvergne, et ai d’ailleurs posé ma candidature pour rejoindre le conseil d’administration de l’association URBH nationale.
Pourriez-vous nous présenter le GCS Blanchisserie du Grand Clermont ?
Dans sa version actuelle, la blanchisserie a été créée en 2008 pour, à l’origine, desservir uniquement les trois établissements du CHU de Clermont-Ferrand. En 2010, elle s’est transformée en GCS et traite désormais aussi le linge des CH Guy Thomas à Riom, Eugène Clémentel à Enval, et Sainte-Marie à Clermont-Ferrand, ainsi que celui des 8 EHPAD du CCAS de Clermont-Ferrand – soit entre 15 et 16 tonnes/jour, toutes typologies de linge confondues. Opérée par 63 agents, elle dispose d’outils de production entièrement automatisés, disposant par exemple – et c’est là une particularité notable – d’un stockeur dynamique alimenté par robot. Autre spécificité, il s’agit de l’une des dernières blanchisseries hospitalières de France faisant l’objet d’un bail emphytéotique, avec un partenaire chargé de la maintenance de ses équipements et de la gestion de son parc immobilier.
Quels projets avez-vous portés depuis votre arrivée ?
J’évoquerais en premier lieu tout ce qui a trait à la responsabilité sociale et environnementale (RSE), qui représente une tendance de fond dans le monde de la santé. J’ai ainsi mené plusieurs actions dès mon arrivée pour réduire notre empreinte environnementale, avec déjà des résultats tangibles. Par exemple, en revoyant le réglage des brûleurs et en limitant le chauffage lors des périodes d’absence des équipes, nous avons pu réduire nos consommations énergétiques de 17 % en un an seulement. Les consommations d’eau en usine globale sont pour leur part passées de 5,7 litres à 4,6 litres, grâce à l’abandon de la lessive en poudre au profit de la lessive liquide, et surtout à la rationalisation du taux de chargement des alvéoles lors du tri du linge. En matière de réduction des déchets, nous avons confié à une structure de réinsertion, la transformation des draps réformés en taies d’oreillers, avec déjà la production d’un premier lot de 5 000 unités. Il nous a en effet semblé dommage de jeter des textiles qui ont conservé la majorité de leurs caractéristiques de tenue, alors qu’ils pourraient servir d’autres usages.
Auriez-vous d’autres pistes sur cette question spécifique des déchets ?
Toutes les blanchisseries industrielles sont forcées d’y réfléchir : bien que nous ne soyons pas encore directement taxés sur les volumes de déchets produits, les coûts d’évacuation ont explosé et nous imposent de chercher des alternatives. Plusieurs options existent aujourd’hui pour la valorisation des textiles réformés, y compris en décomposant les fibres par cardage afin de récupérer la matière première. Mais les coûts de récupération et de transformation sont actuellement refacturés aux blanchisseries, qui ne bénéficient ici d’aucune aide financière. Valoriser nos déchets textiles augmente, in fine, nos coûts de production, ce qui n’est clairement pas incitatif. Et ce sont loin d’être les seuls déchets produits par nos activités ! Ainsi, en 2025, nous essayerons de supprimer les emballages plastiques dans lesquels nous sont aujourd’hui retournés les bandeaux de nettoyage des sols, gorgés d’eau. En remplaçant les modèles existants par des bandeaux ultra-fins, dont les capacités de rétention de l’eau sont donc sensiblement moindres, nous pourrions envisager de nous passer de ces sacs, qui représentent 8 tonnes de déchets par an.
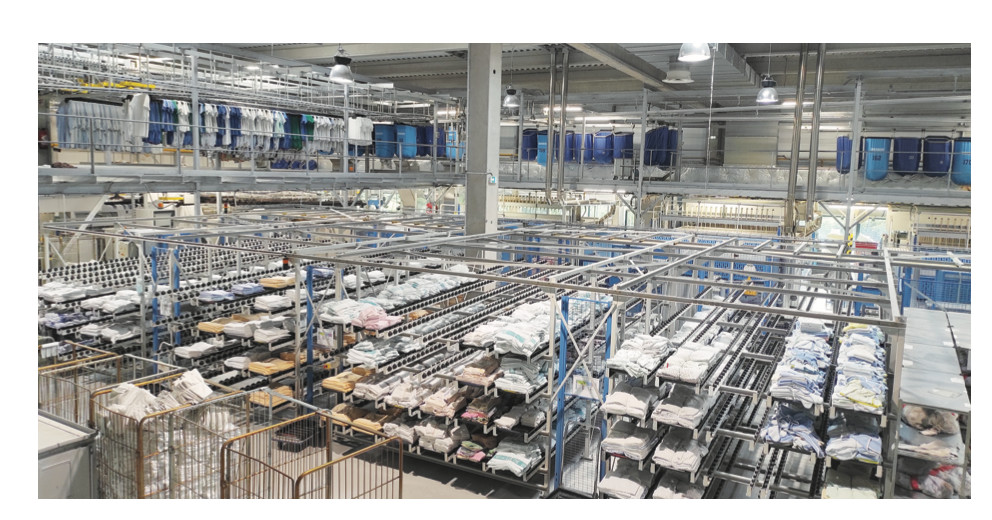
Quid de vos actions en faveur de la qualité de vie et des conditions de travail des agents ?
L’automatisation de nos process permet déjà de considérablement limiter les risques de troubles musculo-squelettiques. Nous avons néanmoins testé l’usage d’un exosquelette pour réduire le port de charges lourdes, mais nos agents n’y ont pas adhéré. Fin juin, nous nous sommes aussi équipés de trois diffuseurs adiabatiques pour humidifier et réhydrater l’air ambiant, asséché par la climatisation. L’environnement de travail est ainsi plus confortable et plus sain, mais aussi mieux adapté aux textiles, qui sont plus difficiles à travailler lorsque l’air est trop sec.
Quels sont vos projets pour 2025 ?
Nous réfléchissons aujourd’hui à la manière dont nous pourrions exploiter les données produites au cours de la production, afin de mieux anticiper les besoins et rationaliser les coûts. À ma connaissance, une telle approche n’est pas encore mise en œuvre dans les blanchisseries hospitalières, mais toutes pourraient aisément prendre ce virage car les logiciels d’exploitation existants collectent déjà un certain nombre de données. Nous préparons aussi l’installation, au 1ertrimestre 2025, d’un premier distributeur automatique de vêtements (DAV) au CHU de Clermont-Ferrand qui, nous l’espérons, permettra de supprimer le lavage des tenues professionnelles à domicile. Mais l’impact réel de ce DAV sur notre activité est aujourd’hui difficile à quantifier. Nous étendrons par ailleurs le recours aux tags RFID, déjà largement utilisés pour les tenues professionnelles et dont nous équipons désormais les draps. Nous explorerons également son utilisation à des fins de géolocalisation des contenants. Enfin, nous nous engagerons dans une démarche de certification selon la méthode RABC et bénéficierons, pour cela, d’un accompagnement par un étudiant en Qualité, Hygiène, Sécurité et Environnement (QHSE). 2025 sera véritablement pour nous une année charnière !
Cela fait plusieurs années que vous observez le secteur de la blanchisserie hospitalière. Quel défi principal identifiez-vous à court et moyen terme ?
Essentiellement les enjeux en lien avec la consommation d’eau, à eux-mêmes mettre en regard avec les tensions sur les ressources disponibles. De nombreuses blanchisseries du secteur cherchent aujourd’hui à descendre jusqu’à 1 litre d’eau consommée par kilogramme de linge. Des solutions techniques existent, mais nous sommes limités par la législation française, qui ne nous autorise pas encore à réutiliser les eaux de lavage dans les process, y compris en les purifiant. Cela n’est par exemple pas le cas en Belgique, où certaines structures ont réussi à atteindre 0,5 l/kg, en réutilisant les eaux usées et les eaux de pluie. Certains estiment que la législation nationale n’évoluera pas tant que le prix de l’eau n’augmentera pas. Or l’enjeu ici n’est pas tant financier qu’écologique, il nous faut préserver les ressources ! De nombreuses blanchisseries doivent déjà réduire leur consommation d’eau lors des périodes de sécheresse. Le problème est donc déjà là, il faut trouver rapidement des solutions durables.
> Article paru dans Hospitalia #66, édition de septembre 2024, à lire ici